How are Our Mirrors Made?
OVERMANTELS MIRRORS ARE HANDCRAFTED TO EXACTING STANDARDS BY OUR ARTISANS
CONTINUING THE BRITISH TRADITION OF MIRROR CRAFTSMANSHIP
Each and every Overmantels mirror is handcrafted in our workshops around the country. Hours of labour and love are poured into each order, ensuring the rigorous quality we guarantee. Below is an overview of the mirror making process, giving you a behind-the-scenes peek at the multitude of heritage techniques which come together to create one of our stunning pieces.
woodworking
The first phase of mirror making starts with the wooden base frame. Our frames are milled out of hardwood in our Cotswolds joinery. The timber is cut down into lengths, and then moulded to form the structure of the mirrors through a series of high-speed cutters. If your frame is bespoke, here is where it’s custom journey begins, with the woodworkers following the required dimensions carefully, ensuring you a perfect fit. The skill and precision with which these frame are made are unparalleled, which is what gives our mirrors their longevity, able to survive hundreds of years.
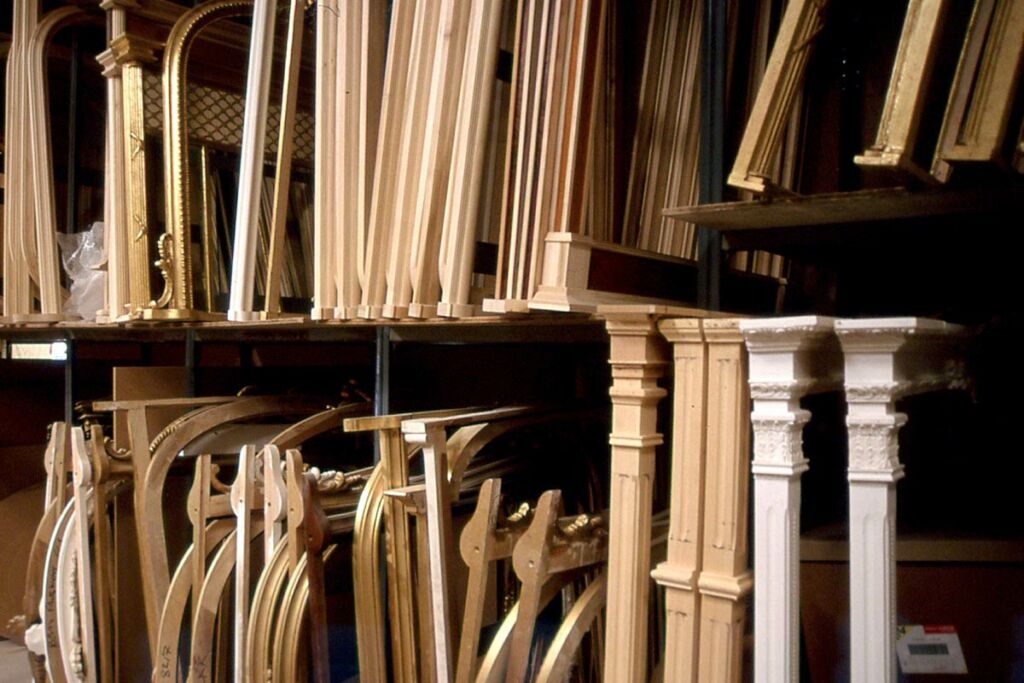
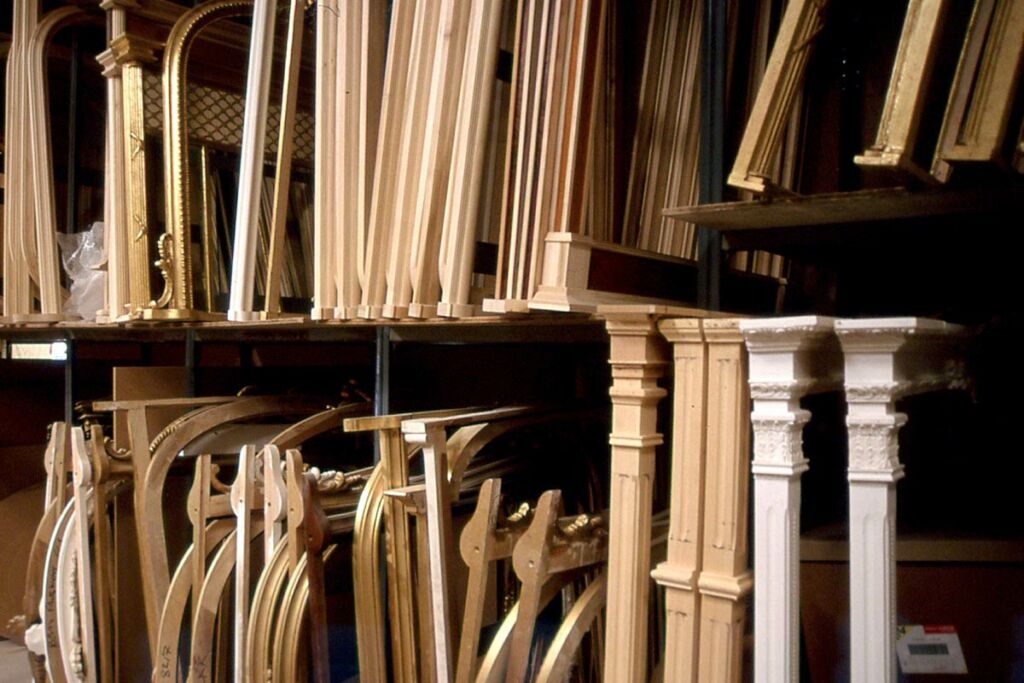
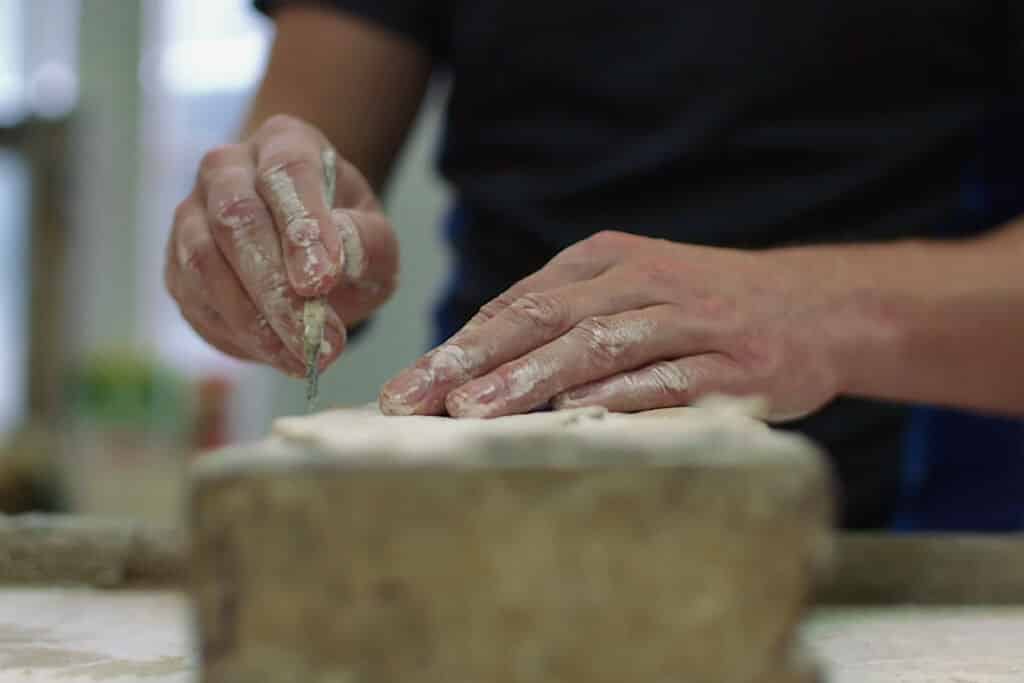
COMPOSITION WORK
The decorative ornaments on giltwood mirrors are made from composition – a flexible plaster-like substance which is pressed into a mould, taking the shape of the carving. Overmantels has an extensive collection of genuine Victorian back-carved moulds, which we still use to this day. When the composition is extracted from the mould, it has perfectly adhered to the shape, giving a crisp and delicate finish. The pressing is then applied to the frame, the flexibility allows it to be manipulated to curve around the woodwork rather than just sit on top as with plaster details. These ornaments must be allowed to cure properly before being applied to the frame, in order to ensure the longevity of the piece.
COMPOSITION WORK
The decorative ornaments on giltwood mirrors are made from composition – a flexible plaster-like substance which is pressed into a mould, taking the shape of the carving. Overmantels has an extensive collection of genuine Victorian back-carved moulds, which we still use to this day. When the composition is extracted from the mould, it has perfectly adhered to the shape, giving a crisp and delicate finish. The pressing is then applied to the frame, the flexibility allows it to be manipulated to curve around the woodwork rather than just sit on top as with plaster details. These ornaments must be allowed to cure properly before being applied to the frame, in order to ensure the longevity of the piece.
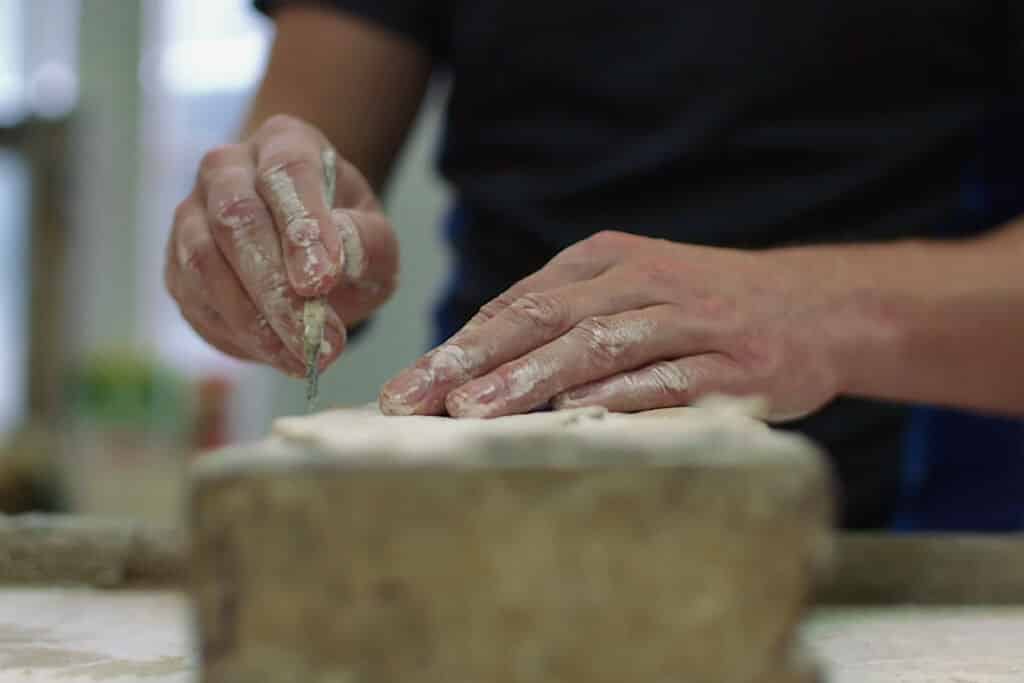
gilding
The next step is to apply the finish to the frame – this is usually done with gilding. First, the frame is prepped with a layer of gesso – a clay like substance which helps the leaf adhere to the base. Then, a layer of coloured bole is applied – this reddish material helps to add warmth to the finish, often appearing through a distressed leaf. Delicate sheets of metal leaf are expertly applied to the frame. This is a painstaking process, as even the slightest touch can render the leaf unusable – we feel very luck to be working with the most talented craftsmen, who have honed their skills over many decades of this work.
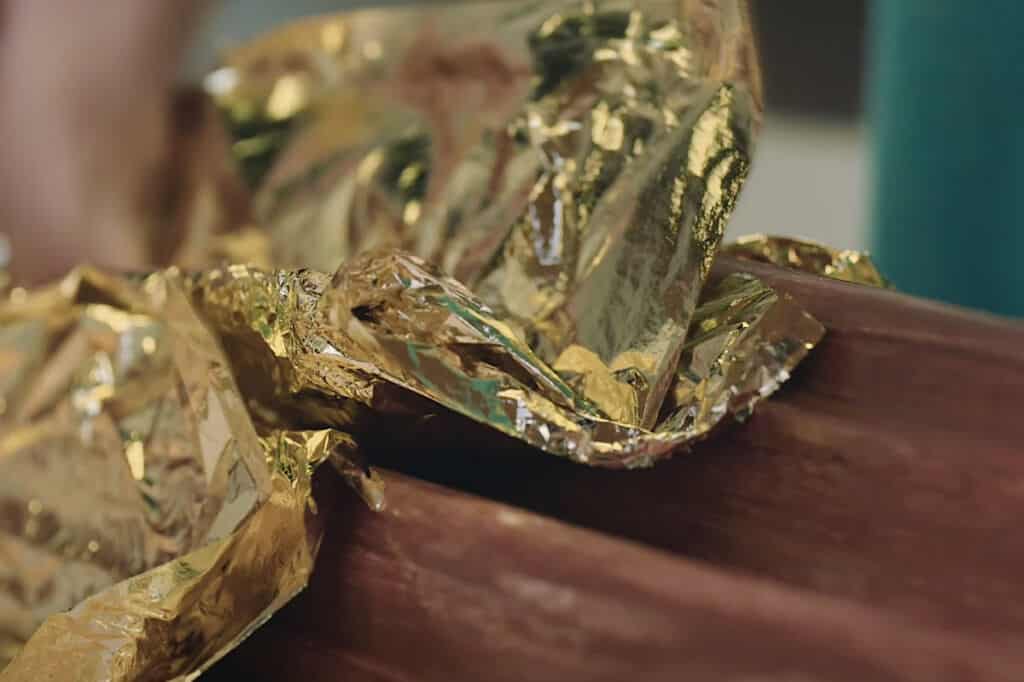
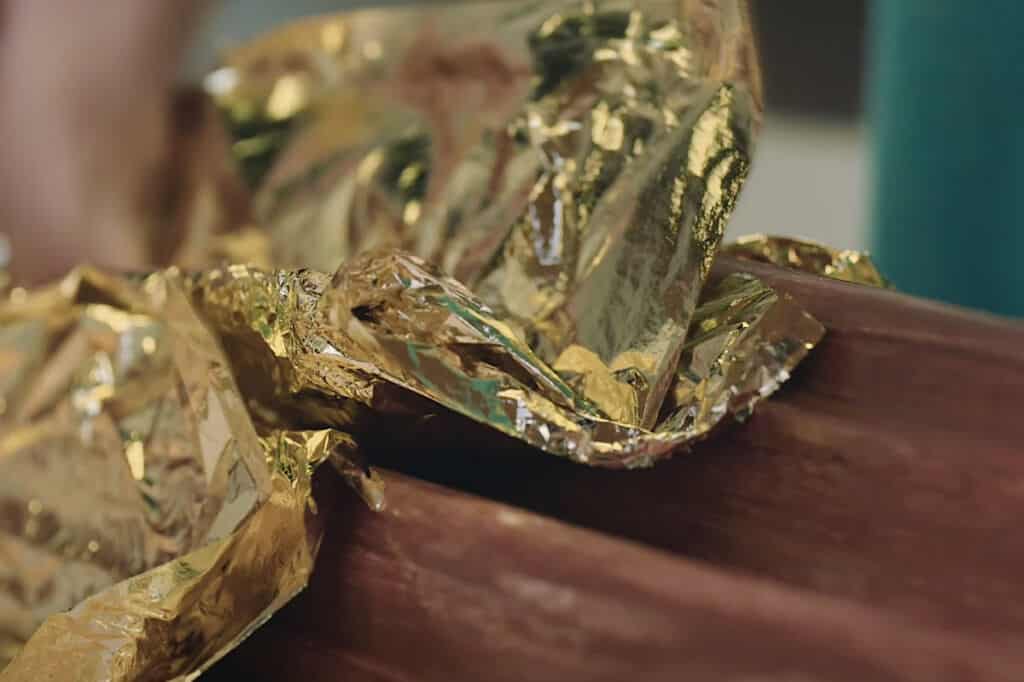
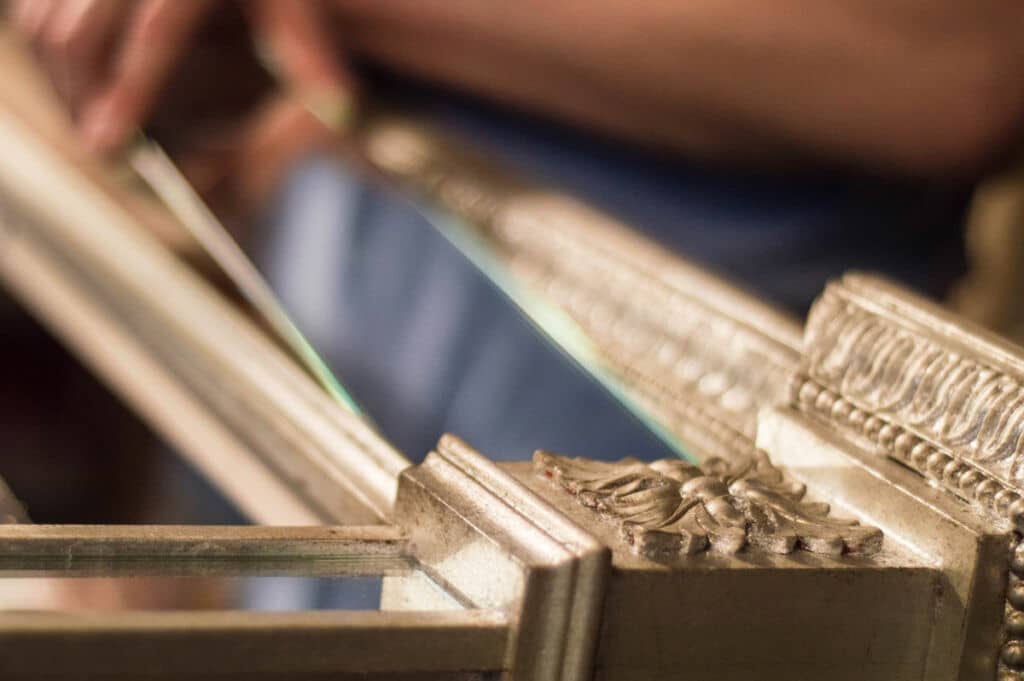
glazing
The final step of the process is to fit the mirror glass. First, we must cut the glass to size with skill and precision – diamond tools must be used to score the glass before the cut. Carefully, the excess glass is snapped away until we are left with the perfect piece, ready to fit to the frame. We prefer to blacken the rebate of each frame, ensuring a clean and sharp edge where the glass meets the gilding. Once the glass is placed inside, the frame is sealed up from the back, securing the glass into place. Appropriate fixings are attached, the whole frame is given a good clean, and checked for quality and accuracy against the client’s order. Finally, the mirror is wrapped up and ready for delivery!
glazing
The final step of the process is to fit the mirror glass. First, we must cut the glass to size with skill and precision – diamond tools must be used to score the glass before the cut. Carefully, the excess glass is snapped away until we are left with the perfect piece, ready to fit to the frame. We prefer to blacken the rebate of each frame, ensuring a clean and sharp edge where the glass meets the gilding. Once the glass is placed inside, the frame is sealed up from the back, securing the glass into place. Appropriate fixings are attached, the whole frame is given a good clean, and checked for quality and accuracy against the client’s order. Finally, the mirror is wrapped up and ready for delivery!
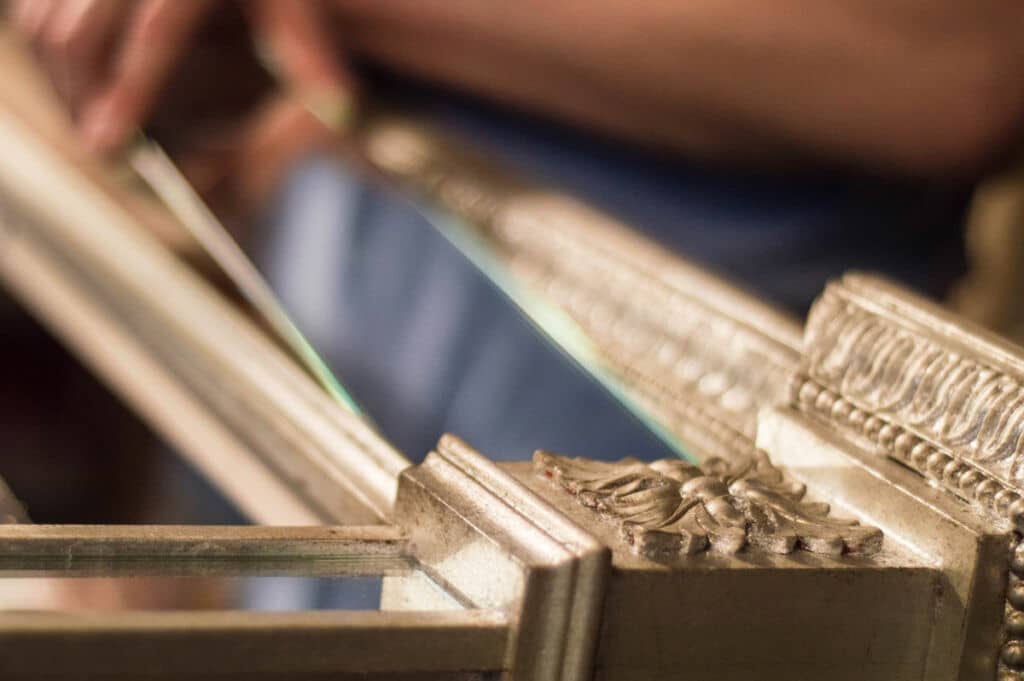